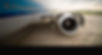
Capabilities
CAPABILITY MEANS IMAGINATION
With over 500,000 total square feet of manufacturing space, we can quickly expand to accommodate larger projects and handle large manufacturing volumes in tightly controlled temperature environments. We use strict certified manufacturing methods and follow outstanding quality verification procedures.

Automation
SEKISUI Aerospace has embraced Automation by adding robots and cobots to the manufacturing process plus developed supervisory control and data acquisition to talk to the equipment miles away. The process that has been created reduces manual data entries from operators and provides individual reports for each part containing process trends, lot info, operator ID, recipe used and start/top time. It also results in reduction of scrap and reduces invalid data due to manual entries. By having trends for each part, it helps identify equipment issues quicker and assist in suspect part investigations.
ASSEMBLY CAPABILITIES VIDEO

SEKISUI Aerospace has seven certified autoclaves:
-
9’ x 16’
-
7’ x 12’ (2)
-
7’ x 26’
-
3’x 20’
-
6’ x 28’ (2)
They all have state-of-the-art computer control over all process variables including heat up rate, dwell time, variable pressurization, controlled cooling and operational limits: 450° and 150 psi.
Autoclave Curing

SEKISUI Aerospace has 15 presses that range from 1 cubic foot to 125 cubic foot capacity. We can heat our tools up to 350° F and apply precise temperature control during manufacturing using Labview. We can also provide pressure and temperature cure profiles at our customers’ demand.
Thermoset Compression Molding/Bladder Molding

SEKISUI Aerospace’s QForge® parts are structurally optimized for strength and stiffness in order to meet and/or exceed metallic versions. Our parts can reduce weight by 40+% as compared to aluminum components – and that is at same or lower cost.
Thermoplastic Compression Molding

SEKISUI Aerospace’s turnkey CCM line produces Thermoplastic pre-consolidated laminates (AKA blanks) from .02 to .40 inches thick and 24 inches wide. We produce from our line with custom ply orientations utilizing automated ply cutting and alignment, welding, and nondestructive inspection (NDI).
Thermoplastic Continuous Compression Molding (CCM)

SEKISUI Aerospace’s Automated Press Cell (APC) uses intelligent automation to stamp form Thermoplastic blanks, which produces continuous fiber structural profiles and forms shapes of varying complexities. The parts are produced at high rates with unparalleled economics.
Thermoplastic Automated Press Forming

Pre Operations
In-House Development & Engineering Team
SEKISUI Aerospace engineers develop composite patterns using CAD tools and cut them using our EASTMAN™ cutters. The machines have the capacity to accurately cut various stacks of material at very high speeds. Rosenthal sheeters are also used to efficiently sheet the pre-preg material.
Laser Projection Systems

SEKISUI Aerospace has the state-of-the-art Virtek LPS-7H Laser projection system used to guide composite lay up operations in our Orange City, Iowa, facility. The new Virtek LPS-7H contains advanced projection and tracking technology that projects up to two times faster than previous laser models. Advanced laser and optical components offer high quality projection patterns and a higher laser refresh rate that minimizes laser flickering. A centralized cooling channel provides thermal stability, enabling the projector to operate in the most challenging environments.
Our shops have three axis, four axis, five axis CNC machines, water jet cutters and lathes. We can design and machine aluminum, titanium, invar or any other material type tools, carbon parts and fixtures. Our machine bed volumes go from 40″ x 40″ x 30″ up to 120″ x 40″ x 30″.
SEKISUI Aerospace can post bond composite structures using high temperature adhesives in precisely controlled furnaces. We can trim parts manually using custom designed trim fixtures or use our CNC machines to trim composite parts or assemblies with outstanding accuracies. We design custom bonding fixtures to precisely bond composite structures together and can perform X-ray scans to verify quality of the bonded joints. Additionally, we can perform X-ray scans to determine attenuation of composite parts for medical applications.

Post Operations – Machining Area

SEKISUI Aerospace clean room facilities feature a 65′ x 50′ CLASS 400,000 with the temperature controlled from 67° to 77° and humidity range controlled from 30 percent to 60 percent. The room is rated with positive pressure with respect to adjoining rooms.
Clean Room Facilities

Paint Booth – Full Priming and Painting Capabilities
Our 9′ x 26′ x 9′ Col-Met semi-downdraft paint booth includes a heat and cure cycle to meet your finished requirements in a fast, reliable manner while maintaining our high quality standards.
-
Moving Paint Line
-
Fill & Fare
-
Batch Painting

Testing and Quality Control
Our team can design custom gauging fixtures, use romers, CNC machines, micrometers, precision calipers and other QC equipment to verify dimensions to within .0001″. We have a full range of inspection and testing devices following ISO 9001:2000 and AS9100:2004 standards.
To learn more about SEKISUI Aerospace's Quality, visit our Quality page.

Flash Thermography
Software for Infrared Thermography Evaluation (SITE) allows SEKISUI Aerospace to measure flaws and anomalies in nonmetallic composite structures, and is currently used for UAV applications. It yields quantitative and qualitative information about shape, size, depth, and location of flaws, anomalies, and bonding in nonmetallic composite structures. It is fast, calibrated, objective and repeatable. Areas of interest can be "zoomed" in on for pixel by pixel analysis. Image subtraction can be used to detect minute changes in bond lines.
SUMMARY OF EQUIPMENT
-
Robots & Cobots
-
Moving Lines
-
Autoclaves (7)
-
NDI Class 400,000 cleanroom
-
Multi-opening Press (MOPS)
-
1000 Ton Press
-
Paint Lines
-
NDI Machines
-
Inspection Equipment
-
Pattern Cutters
-
Test Equipment
-
Flammability Lab
-
Waterjet Cutters
-
Ovens
-
Laser-ply Projectors
-
CNC Machines
-
Tooling Shop
